
Experience
Develop Proactive Maintenance Process at Petrochemical Industry
Unscheduled breakdowns disrupt production processes in many of petrochemical plants. To stop this condition, they wishes to ensure the success of its reliability improvement program through implementation of the needed proactive maintenance process.
This process includes the management of indicator collection activities, the management of equipment indicators big data as well as the management of the resulting alerts / alarm to enable timely identification of the required work order. Thus, Enabling effective asset health management practice.
Proactive maintenance process
1. Collect the Right Indicators that can predict the failure that matters long before it fails.
-
Ensure the right indicators collected correctly at the right time
-
Ensure the infrastructure to monitor this collection process
2. Monitor the indicator properly to identify early potential failure conditions and raise proactive work orders timely.
-
Direct indicators (Check if there is any leak, if yes then repair)
-
Indicators analysis (requiring trending of indicators or combination of multiple indicators)
3. Identify and do proactive maintenance work order timely.
-
Require the workings of good practice maintenance work management process to manage work orders priorities in competing with breakdown Correctives

Figure : Proactive Maintenance Process's Step
Developing asset maintenance & condition monitoring strategy
To ensure achievement of benefit in the long run, it is necessary for the whole inspection program to be derived from a sound reliability based methodology for asset maintenance strategy development.
Hence the inspection program will be based on recognized and credible failure modes rather than based on owned tools or technology. As such we will use the renowned RCM methodology to firstly develop the right predictive strategy as part of the total asset maintenance strategy.
For the development of this program, we will require the contribution of Client's knowledgeable resources to be involved in an RCM analysis work. We will also provide templates from our experiences to speed up the analysis. Utilizing our extensive experience in facilitating asset maintenance strategy development thru RCM methodology, our approach will be as follow:
-
We will group the assets within the scope based on the asset type. This will include all assets in ammonia, urea, and utility plant of kaltim 2.
-
For each of the asset type, we will define its primary and other important functions to ensure comprehensive failure modes generation through functional failure definition.
-
We will then define all credible failure modes to derive the respective failure management strategy. To ensure comprehensiveness, we will also look at sources such as the OEM manual, previous historical record, and suggested PM program. Especially important, we will be focusing also on those failures which have caused plant losses.
-
The listed failure mode will be reviewed for possible adjustments for a specific asset which may have a different operating context or brand name.
-
Lastly, we will facilitate the Client's technical team to analyze together to find the most appropriate maintenance strategy that is technically feasible and worth doing. Focusing on the generation of predictive maintenance tasks which would yield sets of indicator measures for predicting Kaltim 2 failures.
-
The resulting maintenance strategy will then be packaged for CMMS and the resulting condition monitoring tasks will be derived further for indicators and their alarm values.
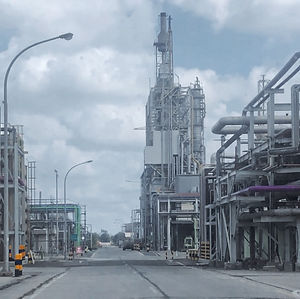
Process & System Setup
​
Following PKT’s team evaluation of the required infrastructure options, the first step in this phase would be to have the technical team install the chosen system hardware, application and additional software required. While the application setup will be done by the technical team from the chosen software vendor, we will oversight the installation and setup to make sure it is as per our best practice design to be used in proactive maintenance process.
Configuration & Define Indicators
​
Once the infrastructure is setup, we will then begin the configuration process starting with setting up the indicators prescribed in phase 1 into the system. Setting up the alert and alarm levels which will be the main vehicles for asset health monitoring and management. At this step, we will also design the proactive maintenance process based on the features and capability of the chosen system. The proactive maintenance process design will include role designation in the current PKT maintenance & related organizational function. Once the process and roles are defined, then we will continue with the configuration of the system to ensure effective business process workflow.
Implementation
​
Completing the configuration of the system and infrastructure, we will then ready for implementing this new process into the organization. The implementation process firstly starts with socialization to those within the organization with this new process. As the sustainability of this process is very much dependent on the degree of commitment of those involve in the process to faithfully execute the inspection program faithfully, Organizational Buy-In is very important. As such, we can not over emphasize the required high level management commitment for proper change management.
People will only do what they are measured. To ensure achievement of the benefit promised by this process, we need to ensure the KPI set we design to be implemented drives the behavior of the people involved long into the program to sustain it. As the inspection program will not bring any benefit if the resulting identification of proactive work orders not executed, we would need to ensure the proper management and prioritization of maintenance work order backlogs. As such, for the controlling and monitoring of this program, the KPIs should also be integrated to include the KPIs of good work management process implemented in 2016. (This includes Backlog, schedule compliance, PM compliance, reading compliance, WO ratios, etc.)